
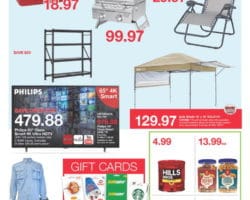
It costs £40,000, which is a lot of cash, and that extra £10,000 would be very handy.It's almost perfect for us, but there are a bunch of small reasons against it. One option is to buy the M75 machine from Datron. Just my 2 cents.It's a good point, and I'm only considering it as one of a couple of serious options. I know you guys are robot designers, but unless you need some really unique feature don't reinvent the wheel. If you're absolutely intent on building your own, then I'd look at the commercially available units that do what you want (Datron, etc) and copy what they're doing for motors, linear motion, etc. I'm all for DIY efforts, but if this is to satisfy a business requirement then just buy the machine and start making your parts. Look for a high quality, used/reconditioned VMC with a high speed spindle. If that's truly your budget, why even consider building your own machine?
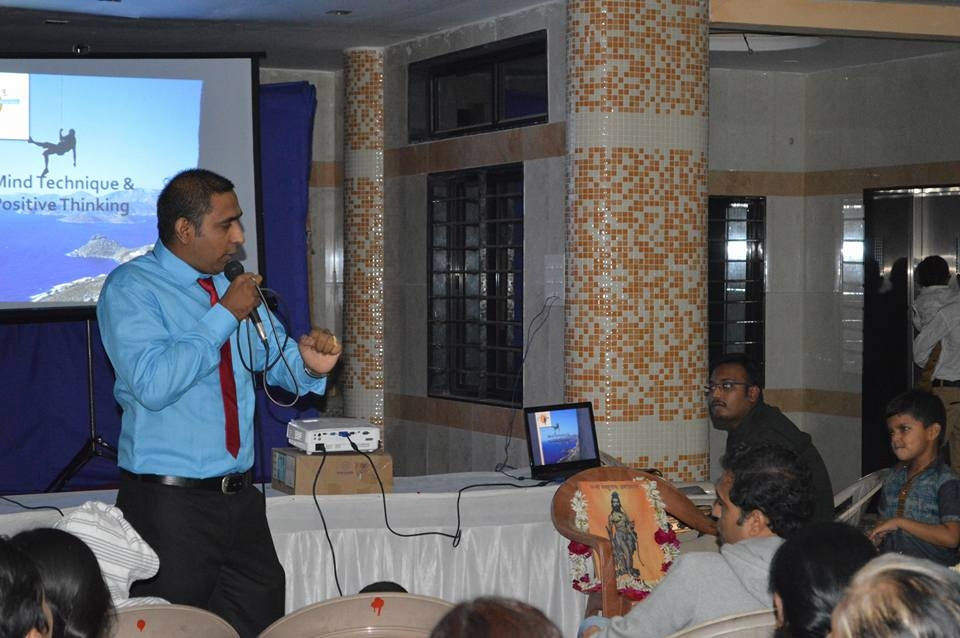
Both the torque and speed requirements easily fall within what can be expected from a 3A / phase step motor run from a 24VDC supply. The motor would only have to deliver 400 RPM at your required speed. If you plan to use a leadscrew and step motors, a 5mm thread with a 58mm (NEMA-23) motor will easily give 1.25 kg of thrust using a very mild 1nM holding torque motor. It makes the power required much smaller and the stress on the mechanism much smaller. The reaction force would be only 10kG spread over 35ms, a far more tolerable situation. How well will your mechanism react to a 100kG reaction side-thrust for 3.5 mS? It would be like a hammer blow.ģ.3W mechanical gives 35 milliseconds to 2m/s and is 0.1G acceleration. Take into account Newton's Law: For every action, there is an equal but opposite reaction. If the load is frictionless meaning all mechanism thrust is invested into 1G of acceleration, you will achieve 2m per minute from a standing start in about 3.5 milliseconds. It requires 33W mechanical to provide 100kG of thrust at 2m per minute.
Emco concept mill 105 datasheet professional#
We have a professional machine builder who will assemble it for us.
Emco concept mill 105 datasheet plus#
The largest tool we currently use is 4mm dia.Īll the parts plus labour comes to less than £30,000. I would like to achieve an accuracy of 10um. The machine I'm spec'ing is similar: Granite base, 30,000rpm 2.2kW Colombo spindle with ATC, 20m/min, same work volume, Aerotech brushless linear motors for all axes, Renishaw 1um encoders, laser tool height measurement, THK linear bearings.
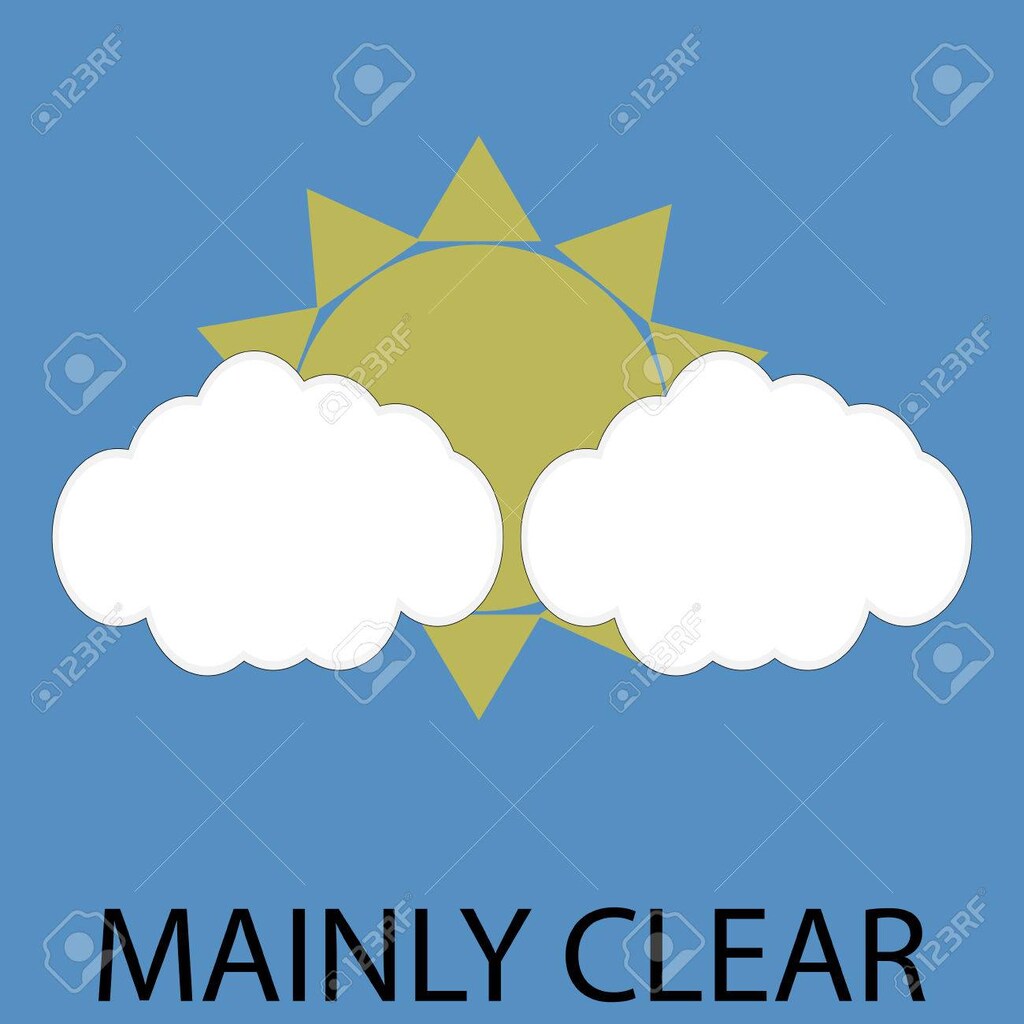
The Datron M75, which is the smallest and cheapest one they do (only just fits in our workshop) has a granite base, 30,000rpm 1.2kW spindle, 14m/min speed.

What I'm trying to do is prove we can build a better machine for less money. LazyMan, that Datron machine is exactly what I have in mind! In fact, a guy from Datron is coming to visit our workshop on Friday. It's for machining Delrin and Aluminium parts for our robot hands. CarveOne, the machine is not for routing PCBs.
